
От идеи до первых форм
Всё начинается с креативных задумок дизайнеров и инженеров. Сначала это – простые цифровые эскизы, а потом – первые объёмные модели. Но не думайте, что это просто «лепка из пластилина». Каждый прототип создаётся с применением современных технологий и материалов, таких как стальные профили, трубки, фанера и полиуретановые панели. Именно из этих базовых элементов формируются пропорции будущего автомобиля.
Мастерство и точность: секреты моделирования
Одним из самых интересных этапов является работа с глиняными моделями. В отделе дизайна мастера «лепят» облик автомобиля, аккуратно добавляя и убирая материал, чтобы добиться идеальных линий. Но до этого момента специалисты технического отдела готовят основу – конструкцию, которая станет каркасом для финальной работы. Звучит как настоящее искусство, не правда ли?
Как работают с материалами?
В цехе хранения материалов находится целый склад, где аккуратно разложены все необходимые компоненты. Представьте себе: узкий, но высокий склад с высотой потолков до 16 метров – это почти как четырехэтажное здание! Там размещается специальный подъемник, который, подобно дирижеру, аккуратно доставляет нужные детали на рабочее место. Если вы любите точные расчеты, то знаете – любая неточность на этом этапе может сказаться на конечном результате.
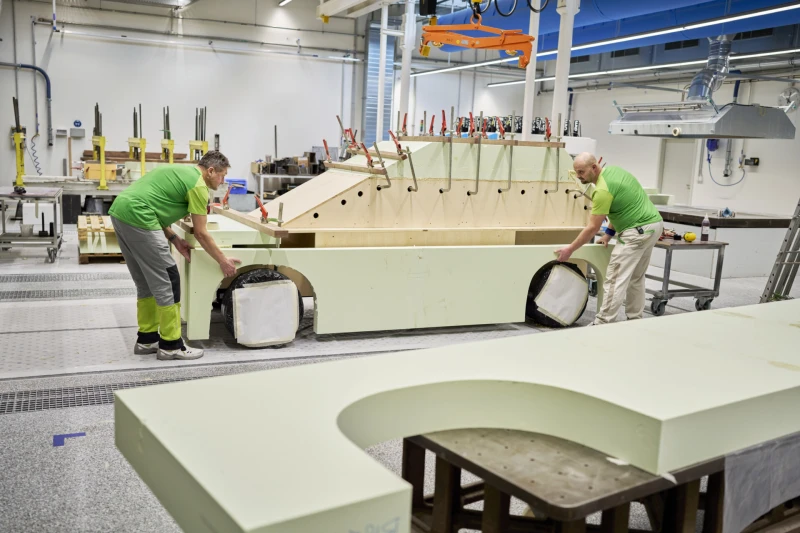
Что там по «волшебным» технологиям?
Здесь не обходится без современных технологий обработки. Для создания «твёрдых» моделей, которые сохраняют свою форму на протяжении всего производственного процесса, используются фрезерные станки. Всего их шесть: три больших для обработки масштабных моделей и три маленьких для изготовления мелких деталей. Эти устройства позволяют буквально за считанные дни превратить цифровые данные в осязаемый прототип.
Изюминка – работа с интерьером
Наряду с экстерьером, здесь создают и прототипы интерьеров. Модели салона используются для оценки эргономики и удобства расположения элементов управления. Специальные технологии, такие как нанесение декоративной пленки и собственное покрытие лаком, позволяют добиться того самого неповторимого стиля и блеска, которые будут присутствовать в серийном автомобиле.
Знакомство с дополнительными «фишками»
Интересным фактом является то, что многие компоненты, например, детали светотехники, создаются прямо на месте с помощью 3D-печати. Представьте, как один элемент может быть напечатан в прозрачном виде, а затем вручную обработан, отполирован и покрыт лаком до идеального блеска! Это требует огромного терпения и внимания к мелочам, ведь каждая деталь должна соответствовать строгим стандартам.

- Проектирование начинается в цифровом пространстве
- Создаются глиняные и твёрдые модели для разных этапов разработки
- Используются современные фрезерные и 3D-печатные технологии
- Отдельное внимание уделяется интерьеру и аэродинамике
Финальный аккорд: контроль качества
Особое место в производственном процессе занимает финальное тестирование. Специалисты проводят точные измерения и проверяют каждую деталь с точностью до сотых долей миллиметра. Здесь даже мельчайшие отклонения корректируются до этапа покраски. Такой подход позволяет добиться идеального соответствия конечного продукта всем техническим и эстетическим требованиям.
В результате на свет появляется не просто прототип, а настоящий шедевр инженерного мастерства, который позже превращается в серийное производство. В этом сложном и творческом процессе участвуют около 80 специалистов – от программистов и конструкторов до технологов и модельеров. Это настоящая командная работа, где каждый вносит свою лепту в создание будущего автомобиля Škoda.
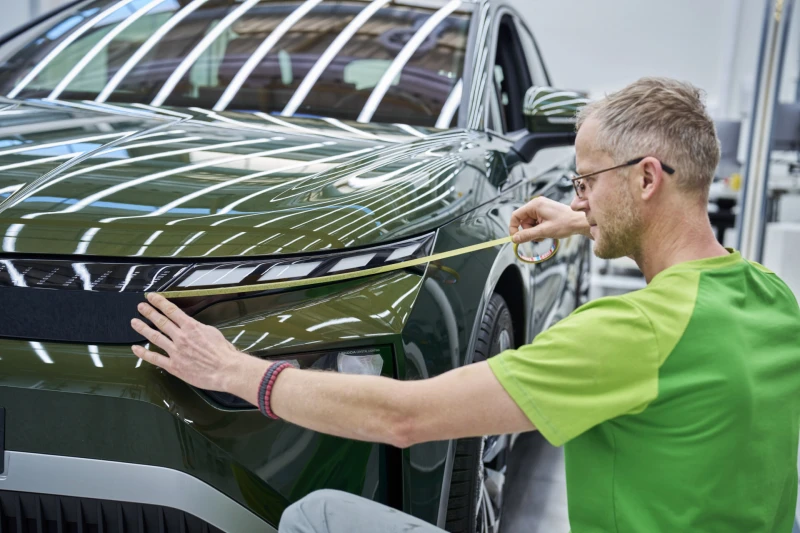
Как видите, за каждым автомобилем стоит невероятный труд, множество технологий и, конечно же, любовь к своему делу. Если вы хотите узнать больше о таких закулисных процессах, следите за обновлениями – мир автопрома всегда полон удивительных открытий!